实力制造
从筹建伊始,汉腾汽车就以全球汽车产业先进标准为依托,以工业4.0智能化管理为目标,全球采购、高度整合,打造欧洲品质标准的汽车生产线,目前已具备完整的四大工艺车间及高性能发动机生产能力。
汉腾汽车产业园一期工程已建设完成高效、完善、环保、自动化生产率高的四大工艺车间,生产设备配备及品质控制水准均达到国内汽车行业主流水平。二期项目已于2016年下半年建设完毕,已形成传统动力汽车、新能源汽车、发动机生产、汽车核心零配件生产四大核心板块。
汉腾汽车作为行业后起之秀,在传统企业运营管理模式的基础上,秉承高起点入门、全球化整合等战略指导,充分吸收借鉴国际国内汽车行业最佳业务实践,在企业战略定位、运营体系、IT、研发、工艺、质量、生产、供应链、物流、人事、行政等业务领域的设计阶段就确立标准化、流程化、信息化、自动化及数字化、智能化的建设方向。目前已全面实现业务信息一体化、业务财务一体化;全面实现企业运用管理的自动化、数字化;全面实现工业3.0水平,部分达到工业4.0水平。
-
冲压车间
冲压车间采用国内外主流设备供应商,选用全封闭式机械压力机生产线,各序间采用瑞士ABB直线七轴机器人和六轴机器人负责板料取送,采用一键换模( ATC )系统,整线换模时间可控制在5min以内,车间关键工序实现100%自动化。 -
焊装车间
焊装车间采用德国KUKA机器人,负责点焊、弧焊、搬运、涂胶、滚边、激光拼焊等工作。总拼采用OpenGate定位切换技术,可实现多款平台车型柔性生产。输送采用Lift Track、EMS、AGV等空中地面三维立体输送形式,快速、稳定、安全,车间综合自动化率90%以上。 -
涂装车间
涂装车间前处理工艺采用先进的无磷硅烷薄膜技术+高泳透力电泳产品,电泳采用分布式直流电源IGBT技术,更节能环保,有效保证产品质量及成本领先;喷涂采用传统3C2B及环保水性漆工艺,利用42台机器人完成整车密封和喷涂作业,关键工序作业实现100%自动化。 -
总装车间
总装车间通过RC、Andon、PMC、AVI等MES系统支持FMS柔性生产。PBS区域可根据生产需求对车型、配置、颜色等进行柔性调整;生产线体采用摩擦输送、升降滑板+SPS、JIT物流技术确保工艺稳定性及物料准确性,采用法国马头伺服拧紧系统对关键扭矩进行跟踪控制及追溯;大型零部件总成采用机械手辅助装配,保证了装配质量及装配效率;车辆检测采用了马勒先进的整车EOL电检技术,动态检测采用宝克先进的检测线技术及新能源安规、动态、充放电等检测,保证了整车出厂质量。
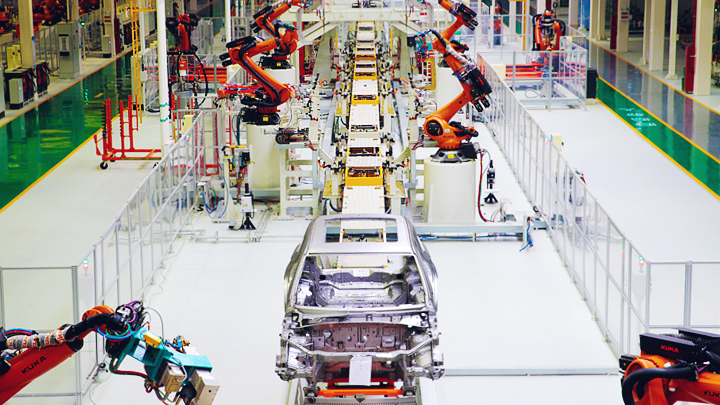
严苛把控 质量要求高于一切
为了提高管理体系的整体有效性,实现标准化、规范化、精益化的管理。汉腾汽车成立之初,就倡导一体化管理体系的建立,目前已确立由(ISO9001-2015质量管理体系、ISO14001-2004环境管理体系、ISO18001-2011职业健康安全管理体系、GB/T23331-2012能源管理体系、 GB/T23002-2017两化融合管理体系 )组成的五标一体管理体系,形成了标准化的科学、先进、有效的管理手段。
早期介入新品开发,积极规避对标车型问题,制定领先同级品质的质量目标,以及创造性地设立8大研发节点质量输出指标;组织供应商培训,签署质量协议;深入制造阶段,洞察用户需求,保证100%整车检测,严格执行“四高”检测标准,即高寒、高热、高原、高盐检测。